Thermoelectric generators can convert heat into electricity, potentially playing an important role in reducing industrial carbon emissions. In a new paper, our researchers have found a way to reduce manufacturing time of thermoelectric materials, achieving a record power output in the process.
Approximately one sixth of all energy used by industry in the UK is emitted into the atmosphere as waste heat. Thermoelectric generators (TEGs), which exploit the Seebeck effect to generate electricity from a temperature difference, could be used to recycle this waste heat into useful electrical energy. They could therefore be vital in helping industry to reduce its fossil fuel usage. Steelmaking, for example, generates vast amounts of heat which could be recycled into electricity, boosting energy efficiency significantly.
However, current commercial manufacturing techniques for thermoelectric materials are energy-intensive and expensive. Tin selenide (SnSe) is commonly used, but producing it requires a high temperature and/or high pressure. As a result, thermoelectrics have not been used beyond a few niche applications, such as in space.
Researchers at SPECIFIC instead found a way to 3D-print SnSe devices, which can be done at room temperature and pressure using relatively low-cost equipment. The technique can also be carried out quickly and easily in large quantities, making it much more viable and affordable for a range of applications.
In another step forward for the field, our latest paper establishes a single-step printing process that substantially reduces the manufacturing time. The method is repeatable, reproducible, and rapid, making it more attractive for industrial use. Furthermore, a proof-of-concept generator made using this method produced the highest power output of any printed Se-based TEG to date.
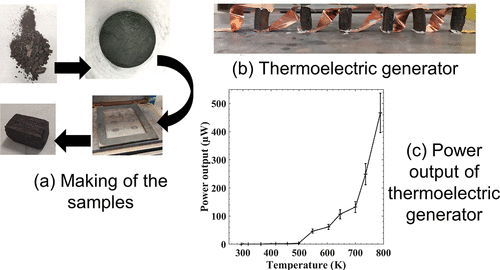
Geraint Howells, lead researcher on the paper and PhD student at Swansea University, said:
“This paper has shown that it is possible to make a cheap SnSe based thermoelectric device that can withstand high temperatures. The power produced by this device is comparable to those within the literature, made by very energy intensive means.”
This research was funded by the Engineering and Physcial Sciences Research Council (EPSRC), the European Regional Development Fund and the European Social Fund via the Welsh Government, Tata Steel, and SMARTExpertise Wales. This funding was received through the following projects: SPECIFIC-IKC, SUSTAIN, M2A, MACH1, COMET, and the SU AIM Facility.