Printed, carbon-based perovskite solar cells (CPSCs) are showing huge promise for commercialisation. They can be fabricated using low-cost, earth-abundant materials, and using the simple, commercially mature screen-printing or roll-to-roll coating processes. However, for this technology to be commercially viable, we have a few challenges to address. Four new papers from SPECIFIC researchers examine ways to identify defects, maximise efficiency, and improve the sustainability of printed perovskite PV, to help pave their way from ‘lab to fab’.
Using microscopy to quantify infiltration
To make mesoscopic carbon-based perovskite solar cells using the screen-printing process, the perovskite solution needs to fill or ‘infiltrate’ the porous structure. The level of infiltration is critical for optimum performance and stability.
However, measuring the level of infiltration between cells has so far been done simply through comparing photographs of samples showing extreme variations.
Instead, our researchers used a microscope and machine learning to quantify infiltration, to better understand its impact performance. As a result, the team could more easily identify issues and develop techniques for improving infiltration, bringing these solar cells one step closer to commercialisation.
Dr Carys Worsley, lead author on the paper, said:
“This method of quantifying infiltration should enable fast, simple, and non-destructive comparison of infiltration at multiple scales. It could be used to improve lab scale performances and for quality control and in-line monitoring in future commercial applications.”
Modifying ink rheology to optimise performance
In this paper, our researchers investigated how the ink rheology, or flow, could be tweaked to optimise the performance of screen-printed CPSCs.
Inks with different solvent concentrations and rheological profiles were assessed using high-speed imaging.
Consequently, the team improved devices by over 10% of the original efficiency. They have also provided key insights into tailoring ink rheology for solar cells and other screen-printed functional films.
Dr Sarah-Jane Potts, lead author on the paper, said:
“When scaling up the size of the devices for commercialisation, larger prints can result in larger problems. These can be overcome by improving the rheological properties of the inks to enable higher quality mesoporous films. This work shows how the ink rheology of the titania paste can be tuned to optimize cell and module performances.”
Achieving peak performance through ageing
Printed carbon perovskite solar cells produced using different solvents benefit from different post-treatments. For example, some cells improve with light exposure while others need humidity exposure to reach peak performance. Understanding the evolution of CPSC devices fabricated using different solvents is therefore key to maximising their efficiency.
In a new study, our researchers found that for CPSCs fabricated with a low-toxicity green solvent, an ageing step was crucial to achieve peak performance. In the days following fabrication, some devices nearly doubled in performance.
These results will be useful for designing processes to scale-up CPSC modules.
Low-toxic hole-transporting materials for roll-to-roll perovskite solar-cells
Another promising method of scaling up perovskite solar cell production is roll-to-roll coating. This continuous manufacturing process simplifies high-volume production, and replacing the gold electrode with carbon has further reduced costs and improved stability. However, there are still scalability and sustainability challenges to address.
In a recent study, our researchers compared four different hole transporting materials for carbon-based roll-to-roll manufacture. They identified the ideal material in terms of efficiency, stability, toxicity, and cost.
The hole-transporting layer transfers the ‘hole’ charges from the perovskite layer to the carbon layer. Introducing a compatible hole transporting layer significantly improves performance. However, many of the materials used for these layers are toxic and therefore harmful to both the environment and those working with them.
Dr Ershad Parvazian, lead author on the paper, said:
“Our work bridges the gap in roll-to-roll scalable production by replacing highly toxic, halogenated solvents with less toxic alternatives for all layers, including the hole transport layer. This research offers key insights into overcoming the challenges of scaling up from lab-scale experimentation to industrial-scale feasibility for a greener approach.”
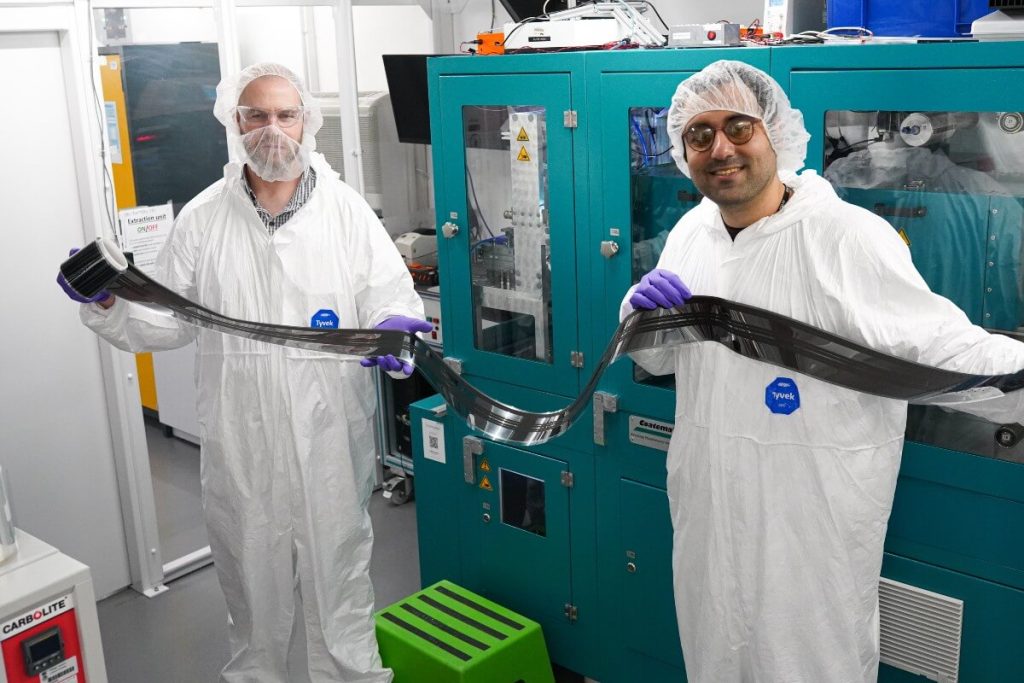
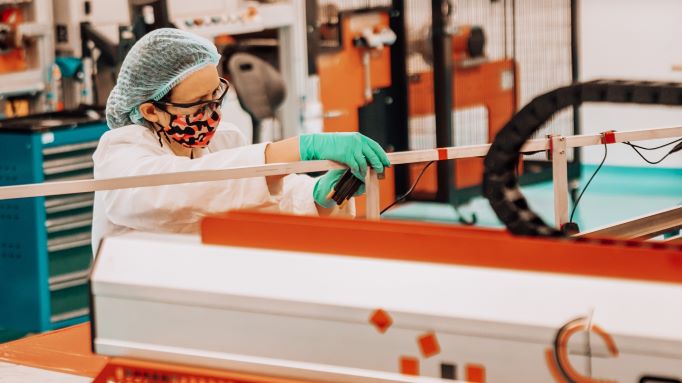
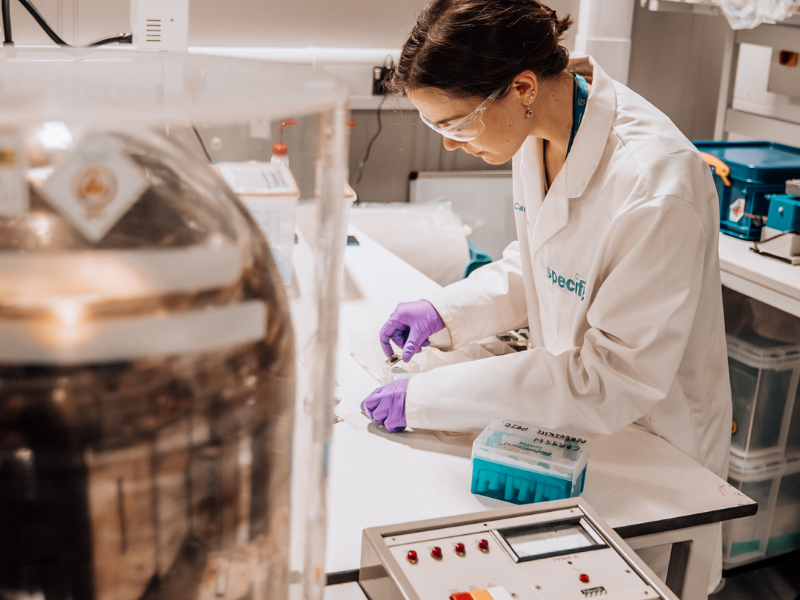