We recently celebrated 10 years of our Pilot Manufacturing Resource Centre (PMRC). Based in Baglan, the PMRC is a world-class research and technology facility that acts as a vital stepping stone for progressing renewable technologies from the lab to factory. Looking back over the last decade, our staff have selected 10 of its most memorable moments.
1. The Opening Event
PMRC’s story begins in 2012 with the completion of the first construction phase. We celebrated the opening of the main structure and some of the pilot line with a launch event attended by Carwyn Jones (former First Minister of Wales) and Sir John Vincent Cable (former Secretary of State for Business and Trade).
PMRC was designed to build on our existing research into coatings, including PV, for steel and glass, enabling the next steps into scale-up and commercialisation. The new processing line would allow for developing new materials and product testing on a larger scale.
Furthermore, with academics and product development specialists working closely together on one site, it would enable ideas to move quickly between the lab and factory floor.
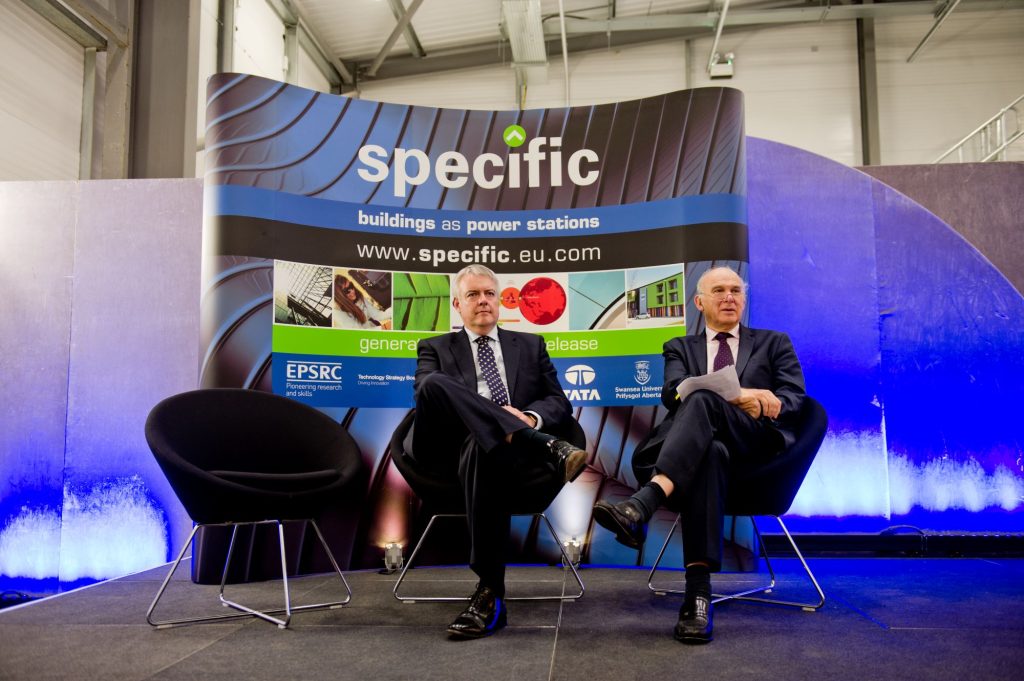
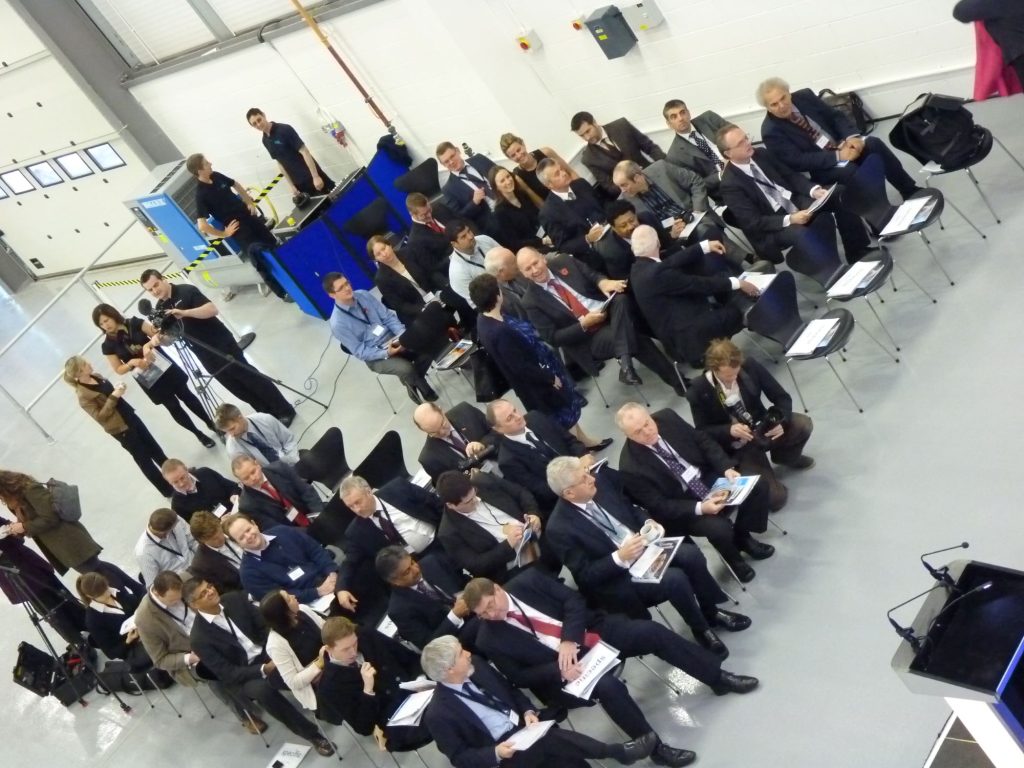
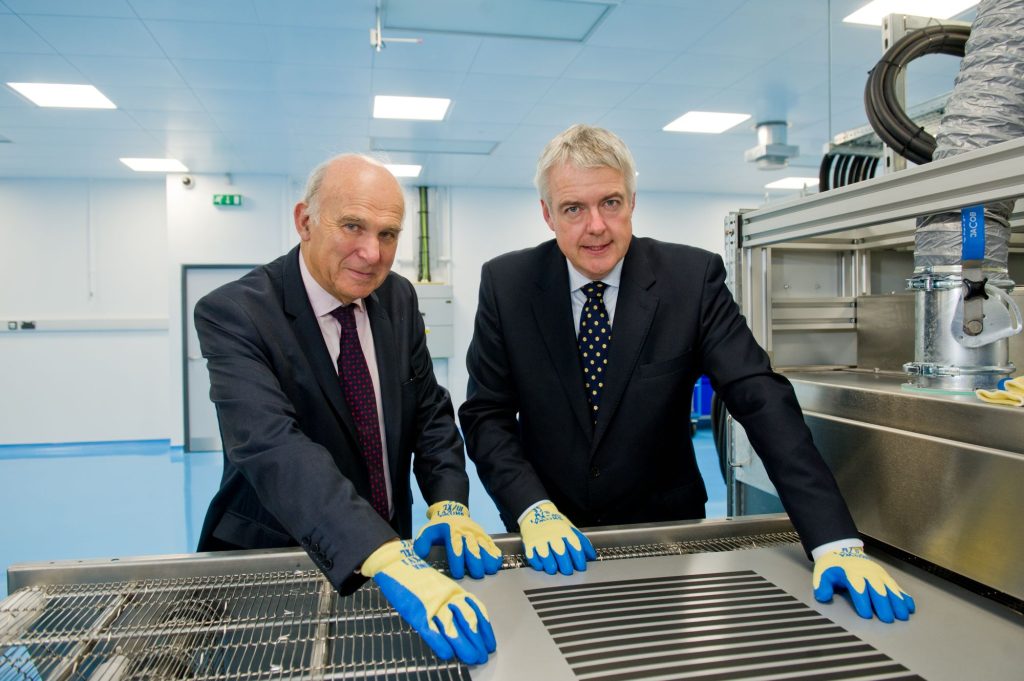
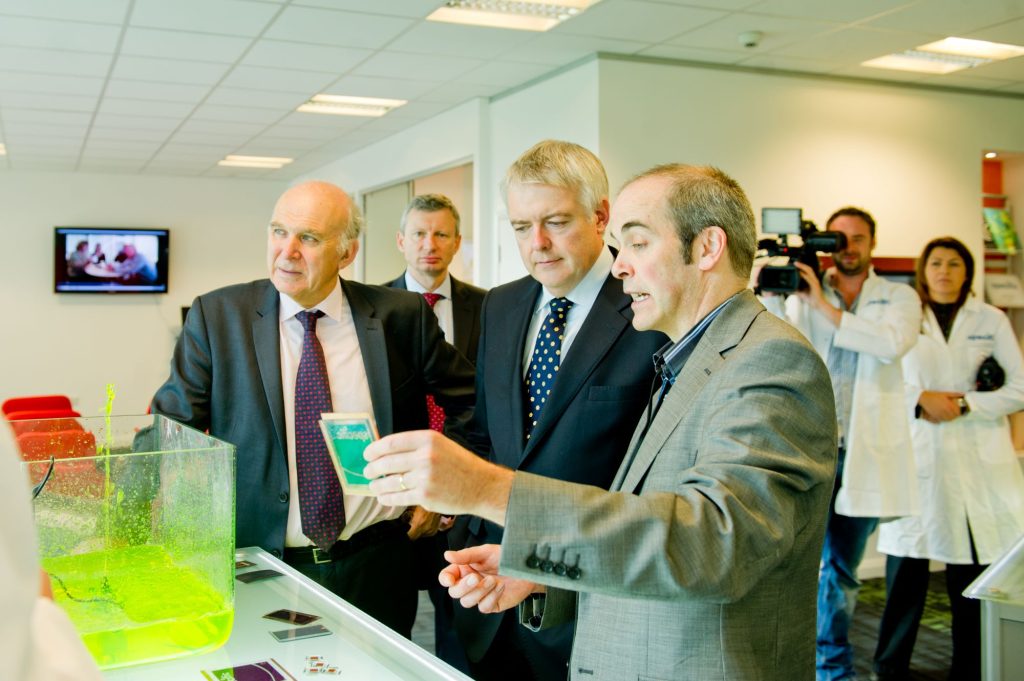
2. Opening the Labs and Cleanroom
The second opening stage in 2014 saw the installation of the cleanroom and labs. This stage was supported by £1.9 million in funding from the Academic Expertise for Business programme. This six-year programme of support from the Welsh Government and European Structural Funds was to support knowledge transfer from academia to business.
Mrs Edwina Hart, former Minister for Economy, Science, and Transport, attended the Phase Two opening event. At the time, Hart said:
“This is an extremely important milestone in the SPECIFIC project and highlights the importance of industrial and academic collaboration in taking forward such highly innovative work.”
Lots of magic happens in the labs and cleanroom, from printing solar cells to curing coatings. We also use these facilities to aid businesses who wouldn’t otherwise have access to our equipment and expertise. For example, we recently supported Advanced Electric Machines (AEM) by coating a batch of laminations for their sustainable electric motors using our industrial roller coater. As a result, AEM successfully built a new prototype motor allowing them to test its performance and demonstrate it to potential customers.
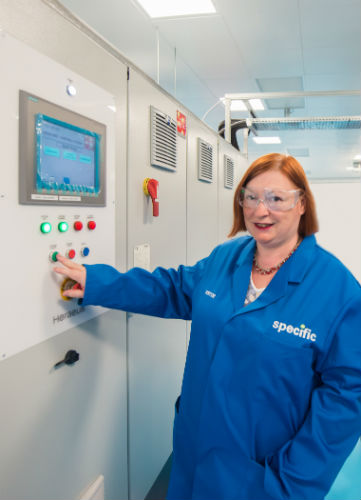
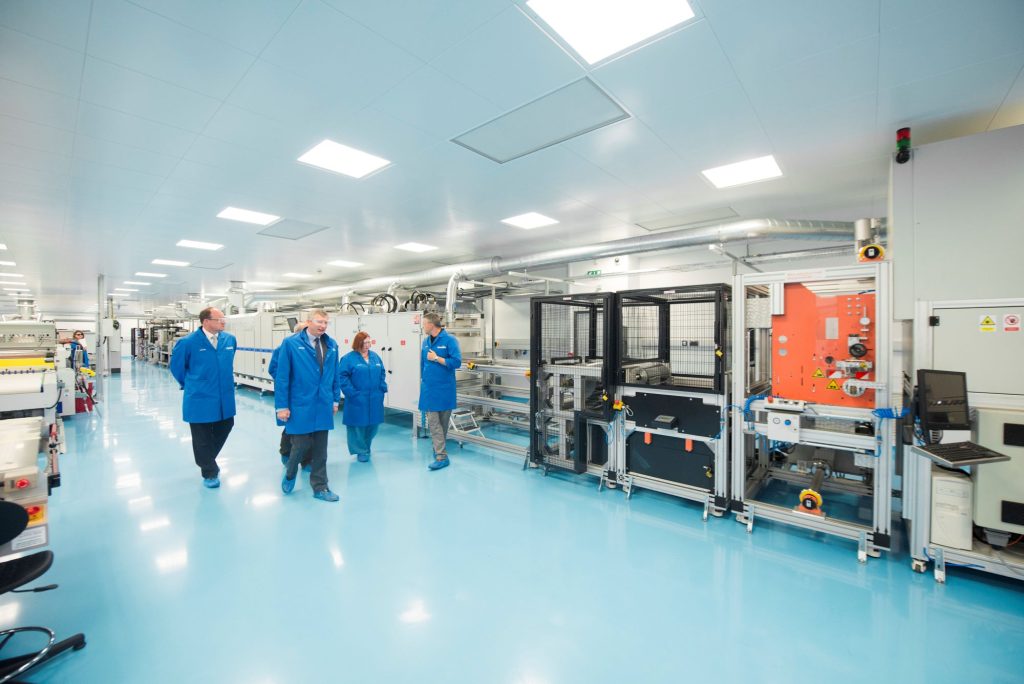
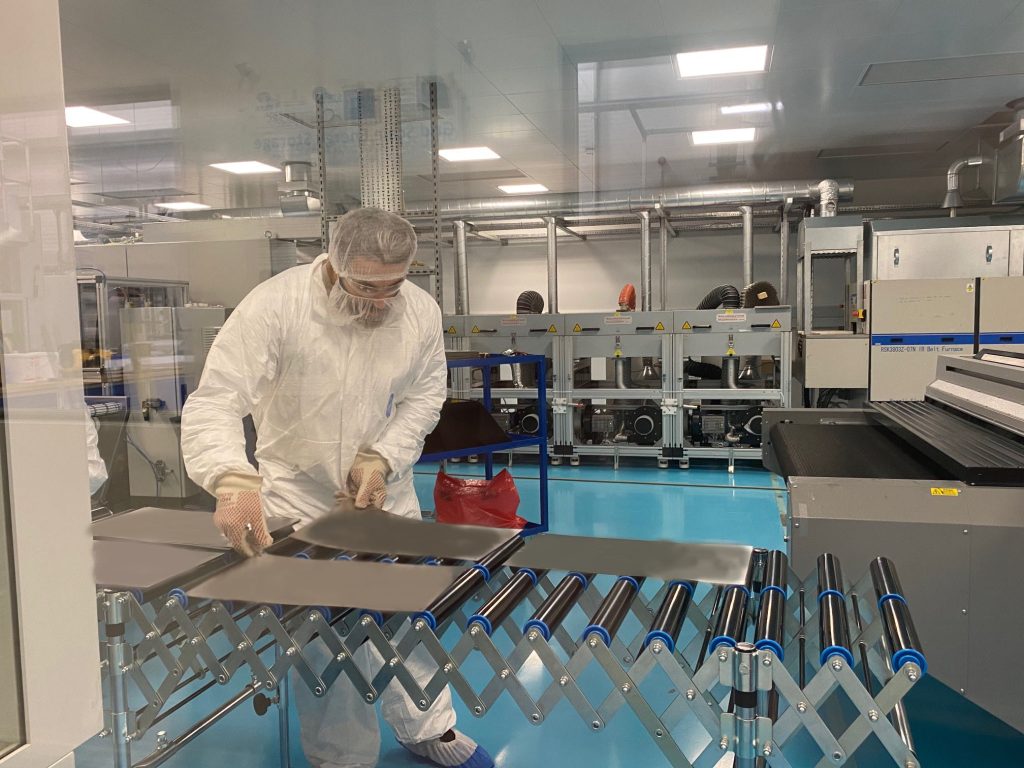
3. Screen-Printing Solar Cells to Travel the World
Some of the most exciting pieces of kit in the cleanroom are the two screen printers, which are primarily used to print solar cells. In fact, our team used them to print the first UK-made carbon perovskite solar modules.
The main advantage of the screen-printed mesoscopic carbon-based perovskite solar cells (C-PSCs) that we make at PMRC is that they are made with a relatively simple, affordable, and commercially mature process that can produce industrial scale devices. Our PV team uses the larger of our two screen-printers to make 30cm x 30cm solar modules.
These larger modules have travelled all over the world:
- In 2021, the PV team printed 12 functioning 30cm x 30cm modules and sent them to Jamshedpur, where they were demonstrated in India for the first time at the Tata Founder’s Day event.
- Then in 2022, the team decided to test the modules outdoors in a South Welsh climate. They mounted six modules on a weathering station at the SHED in Port Talbot to monitor solar performance of the panels continuously for a year.
- Earlier this year, they took three modules to Mexico and installed them on a weathering station at Cinvestav, Merida to monitor their performance in a completely different climate.
Dr Sarah-Jane Potts, postdoctoral researcher in our Industrial Coatings group, said:
“Screen-printing is an ancient technique that is best known for patterning t-shirts. Despite its humble origins, its simplicity, affordability, and commercial maturity make it ideal for manufacturing a range of printed electronics across many industries. These include healthcare, consumer electronics, sensors, as well as sustainable energy generation and storage. As an additive manufacturing process, it also produces less waste than alternative methods, making it a more sustainable manufacturing technique. In our case, screen-printing has enabled us to produce thin film, underfloor resistive heaters, as well as affordable, large scale mesoscopic carbon-based perovskite solar modules, with the potential to go larger.”
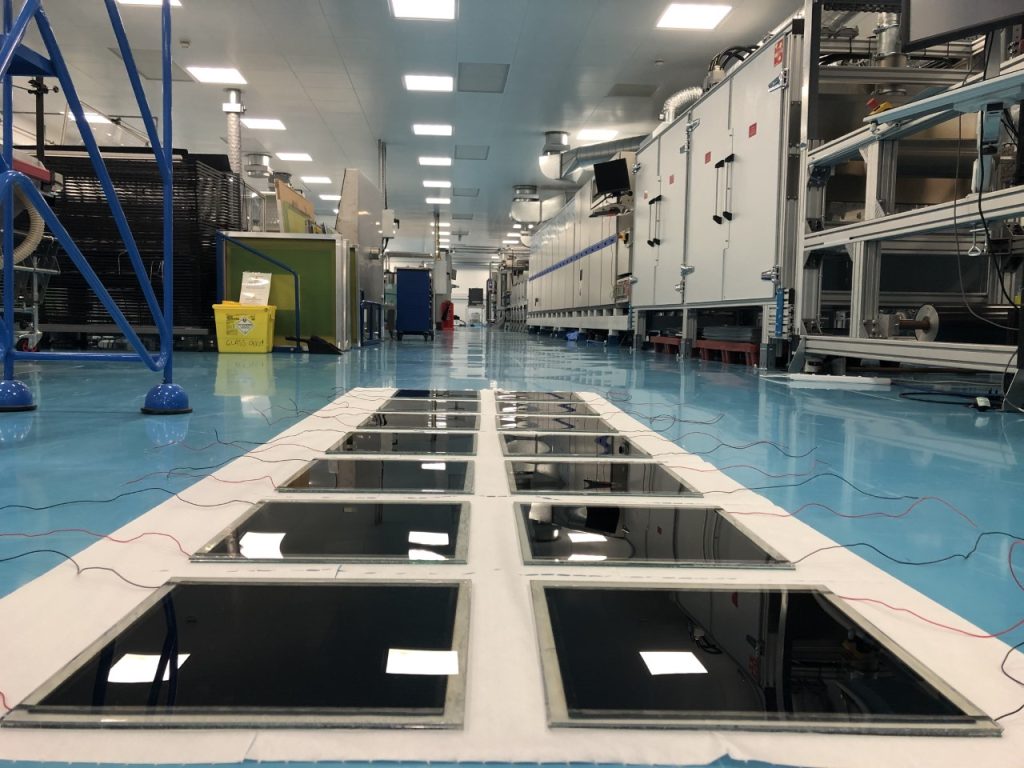
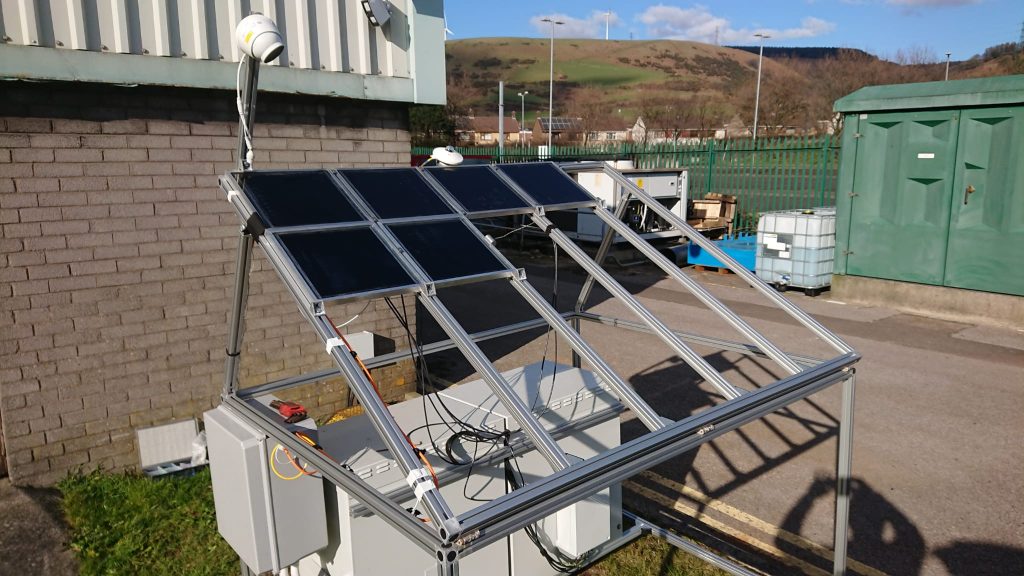
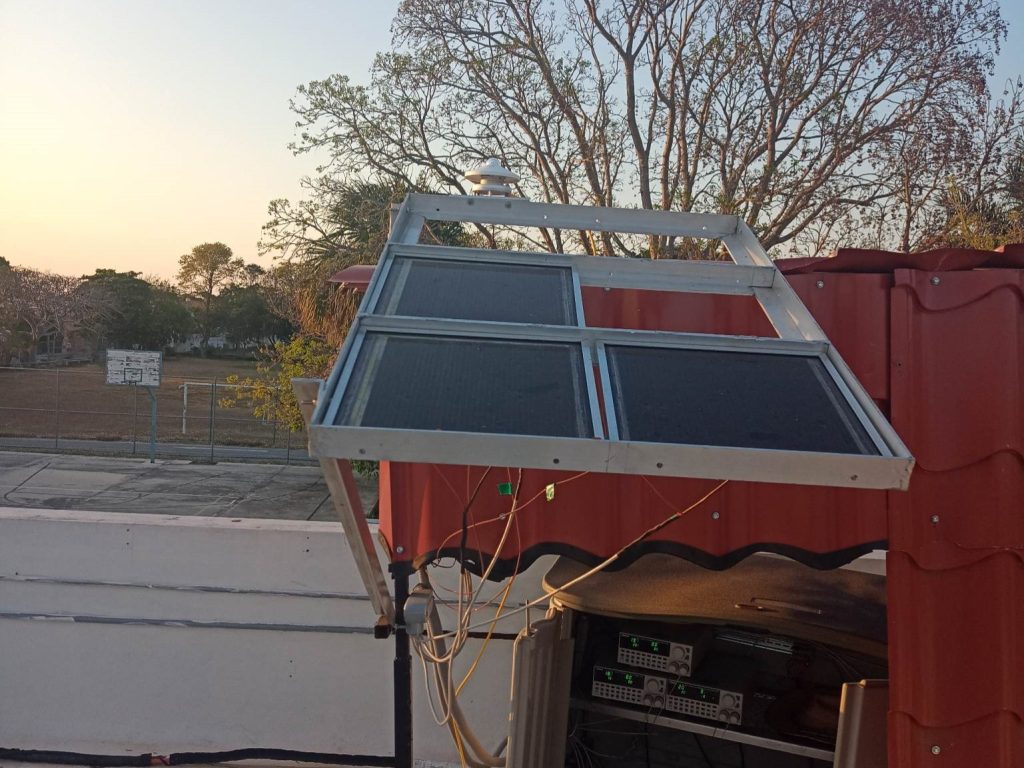
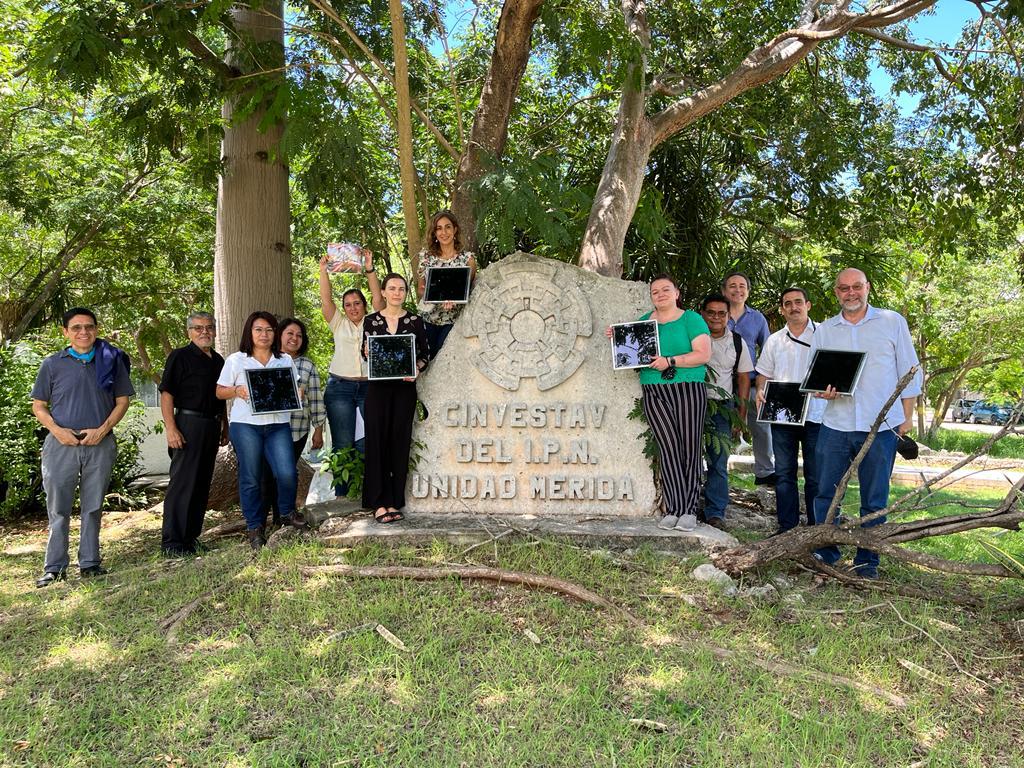
Watch a time-lapse video of Dr Sarah-Jane Potts using the screen-printer to print the carbon layer of the modules:
4. Screen-Printing Heated Floor Tiles
We also used the PMRC’s larger screen-printer to print the electrically-heated floor tiles that we installed in the Active Classroom.
To make the tiles, we printed a conductive ink onto steel sheets which we then bonded to plywood panels. Channels routed in the plywood house electric braids which enable an electric current to pass through the coating providing an efficient form of resistive heating. These resistive tiles are quicker to install than standard heated floor systems, can be applied to raised access floor tiles (ideal for offices and retrofit applications), and ideal for combining with renewable electricity generation.
As the primary source of heating in the Active Classroom’s main teaching space, the heated floor provides electrical heating that is zone-able and adjustable. A control system means that targeted areas can be heated independently from the rest of the building. This same control system also helps to prevent temperature overshoot, maintaining a comfortable temperature when large numbers of people enter the room as well as when the classroom has fewer occupants.

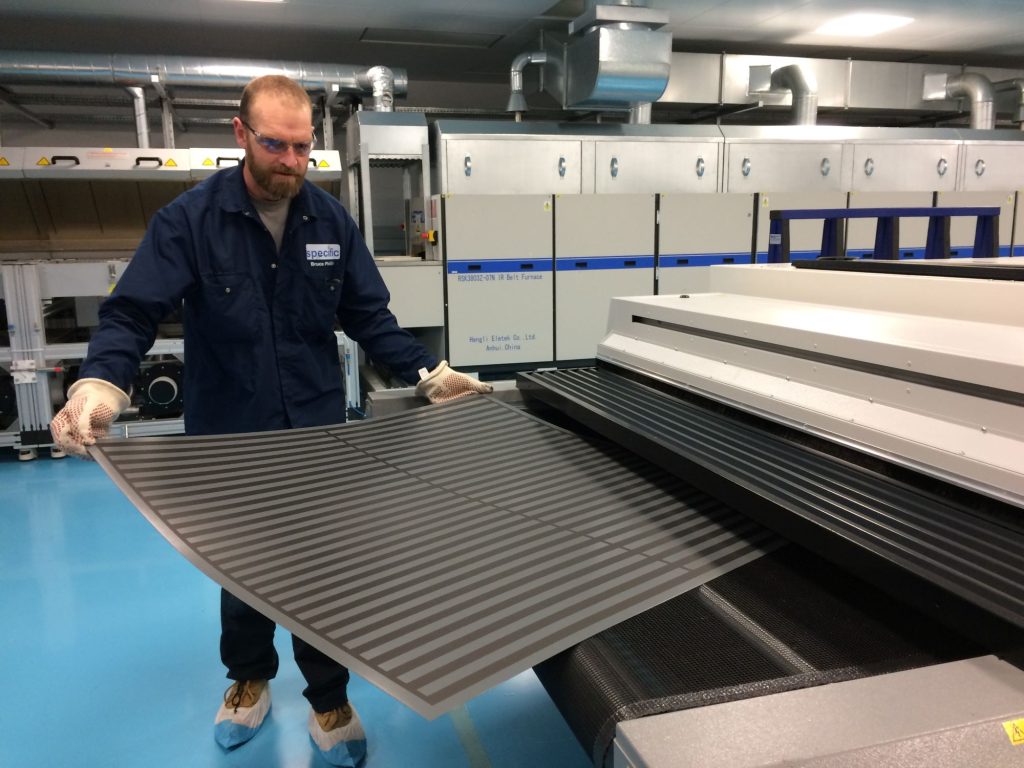
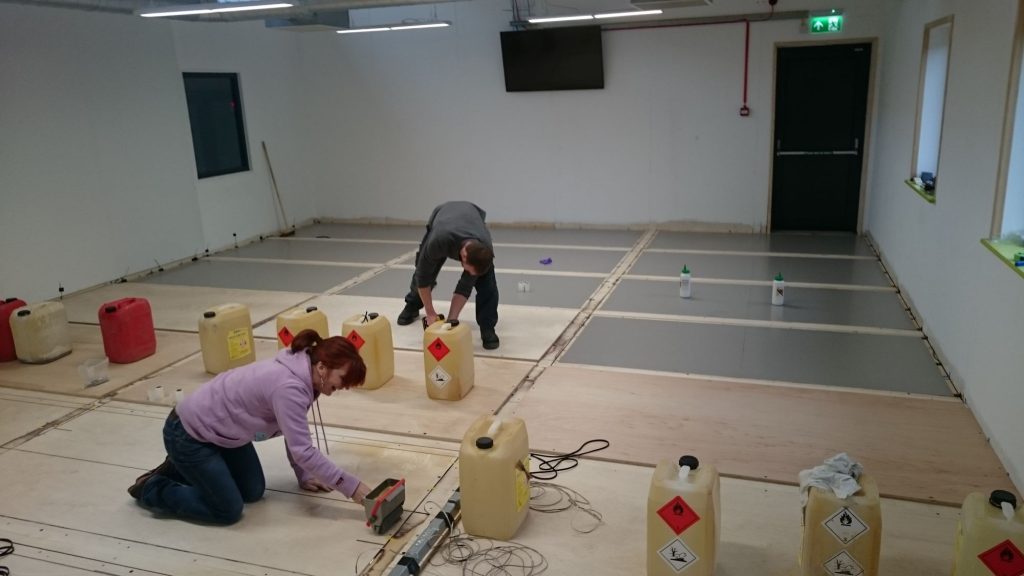
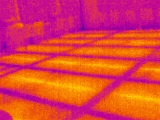
Watch a clip of Dr Bruce Philip and Dr Eifion Jewell screen-printing the floor tiles:
5. Testing Emerging Heating Technologies in the Climatically Controlled Room
In 2013, we installed the climatically controlled room. This is a space where the air temperature and humidity are controlled and maintained, irrespective of external weather conditions.
The room was designed to demonstrate our previously mentioned underfloor heating system. It comprises an inner and an outer room, built with standard stud partitions walls with 100mm insulation and an insulated base. The inner room has a known thermal performance due to temperature logging, and the outer room can be cooled and held at a setpoint temperature by means of a chiller unit.
Though initially designed for demonstration purposes, the room has been repurposed to assist companies developing emerging heating technologies. For example, Thermify, who capture waste heat from data processors and use it to warm homes. More recently, we’ve been testing the efficiency of electrical radiant and infrared low temperature room heaters.
Heat accounts for approximately 50% of total energy consumed in the UK. Around 80% of that is used to heat homes and other buildings, predominantly using natural gas boilers. Therefore electrification of heat, to capitalise on increased generation from renewable sources, brings great challenges and opportunities. Heat pumps are one potential solution but they will not be appropriate in every application. Radiant and infrared heating may be a viable alternative, however, there needs to be a far greater understanding of its efficiency. At the moment, our climatically controlled room does not exactly meet the standards of a certified test facility. We are therefore hoping to upgrade the room to provide a facility capable of testing to the existing standard and to develop additional tests to explain how the results relate to human thermal comfort.
Senior Technology Transfer Fellow Dr Bruce Philip said:
“Radiant heat heats people and surfaces directly without warming the air in between, meaning that you can feel comfortable at lower air temperatures, in much the same way that you feel warmth when moving from the shade to direct sunlight. Understanding the extent to which electrical low temperature infrared heaters are capable of doing this could alter the way we think about providing indoor thermal comfort. If rapid response heating can be provided only where and when it is required it could save a significant amount of energy when compared to more traditional heating.”
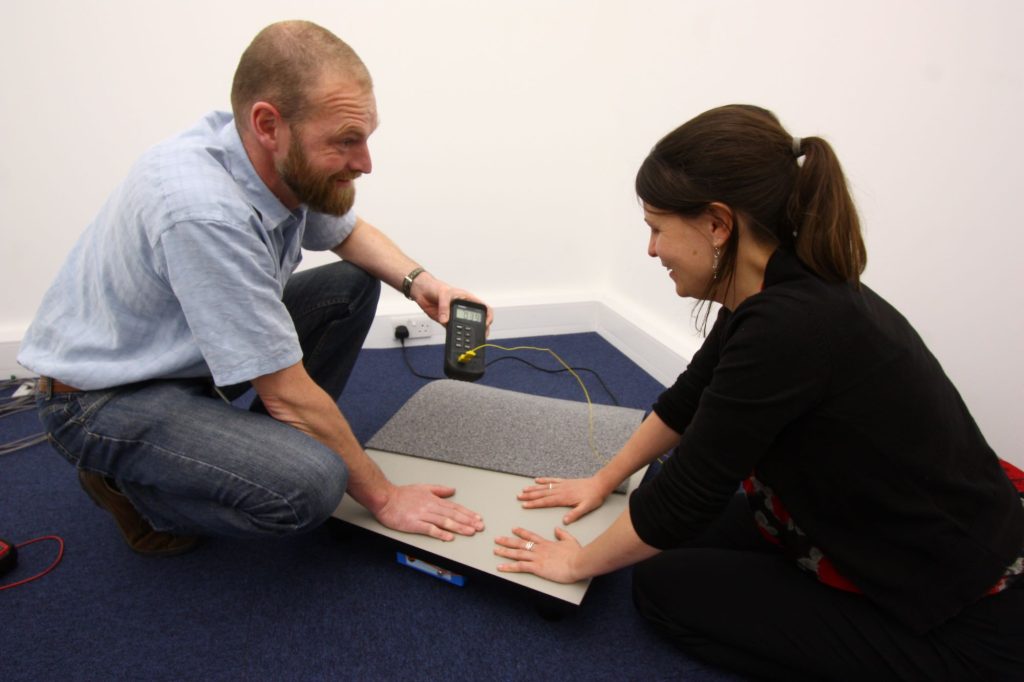
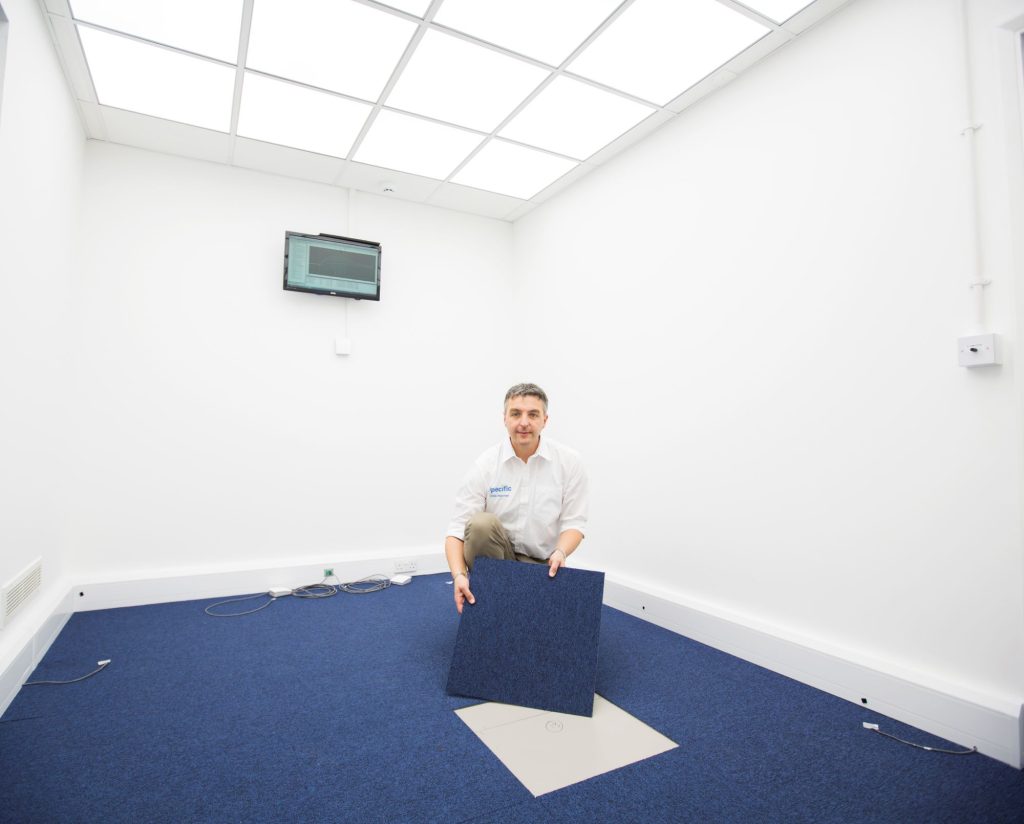
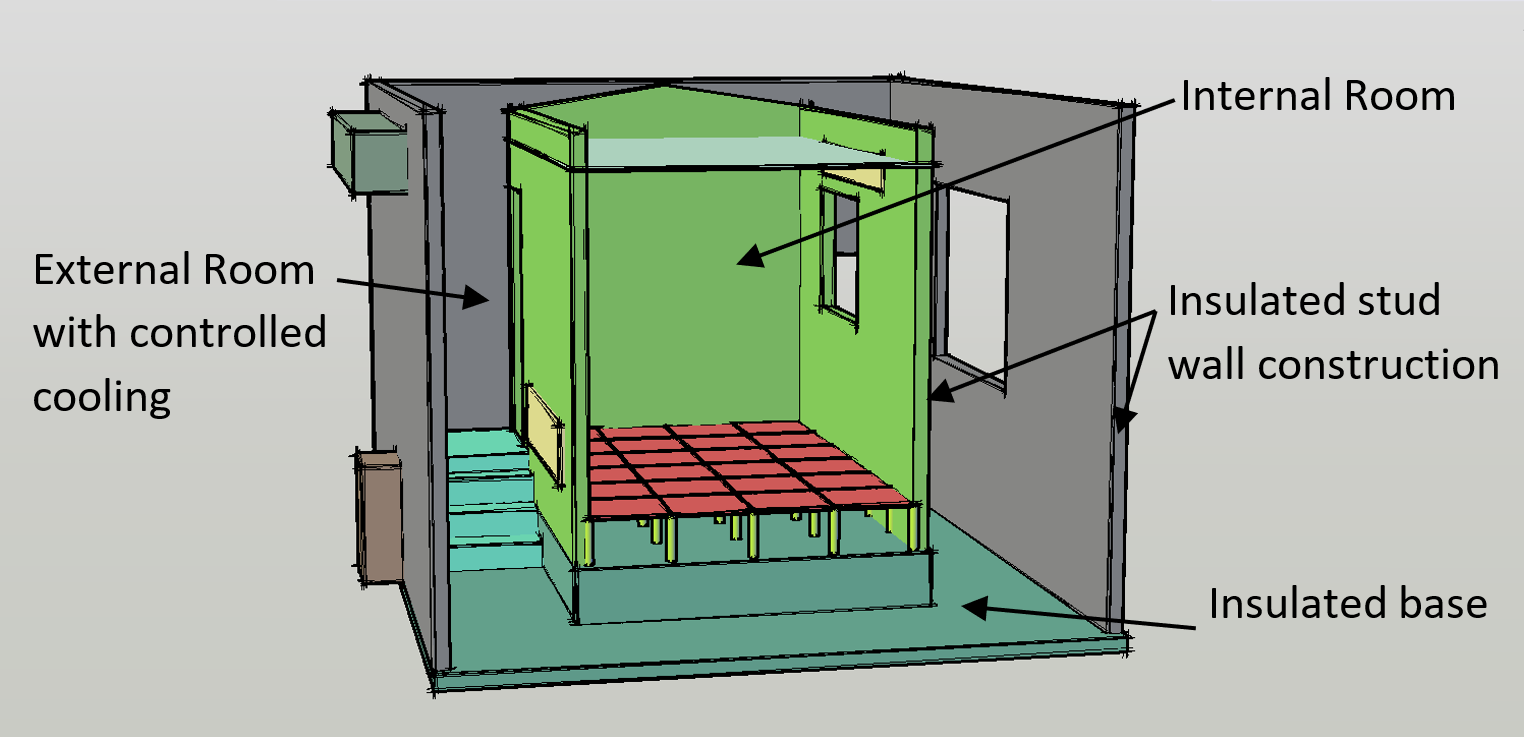