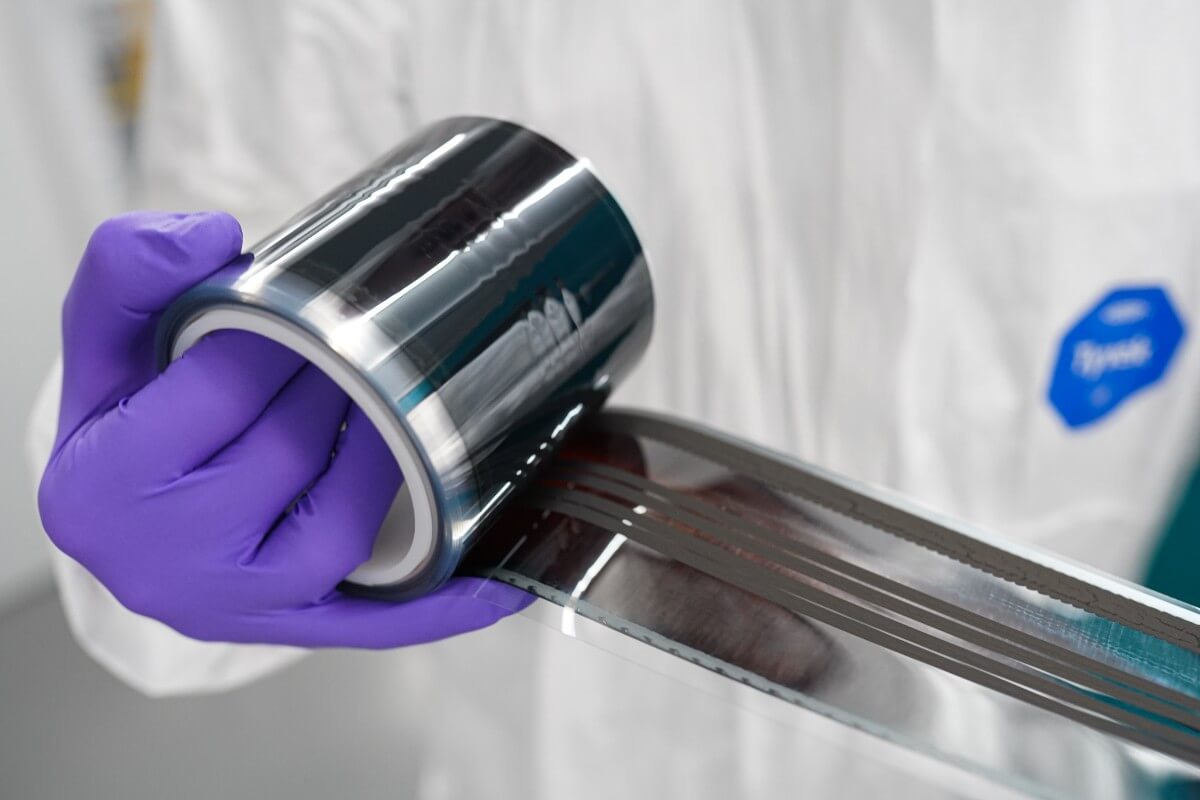
PRINTED PHOTOVOLTAICS
For printed photovoltaics to succeed, they must move quickly from the lab bench to the factory floor. Here at SPECIFIC, our teams are developing a range of solar cell technologies and processing techniques that will allow high-efficiency thin-film printed photovoltaics to be manufactured at scale using earth-abundant, low cost materials.
We are also working to understand the stability and lifetime of these devices, by characterising their degradation mechanisms and finding ways to improve longevity for the ultimate goal of commercialisation.
Our world-class facilities are designed for the scale-up of solar technologies from lab to full-scale. We consider ourselves ‘technology agnostic’, which means that we work with the most promising photovoltaic technologies to find ways to manufacture them at scale. Currently we have research teams working on four distinct technologies at Swansea University: perovskites, CZTS (copper, zinc, tin, sulphur), organic photovoltaics and dye sensitised solar cells.
We collaborate with researchers across the world including Imperial College London, University of Oxford, University of Cambridge, University of Warwick and University of Sheffield.
Printed Photovoltaics Case Studies
World’s First Fully Roll-to-Roll Printed Perovskite Solar Cell
Printed carbon perovskite solar cells have shown huge promise. They have good efficiency and can be produced cheaply and easily with minimal low-cost set up. They also achieve high levels of stability. But there are still some problems that must be overcome before they reach commercial reality.
One of these problems was the gold electrode, which is typically applied after printing using an expensive and slow evaporation process. Using slot die coating in a roll-to-roll process, SPECIFIC researchers established a new low-cost and scalable carbon ink formulation to replace the gold.
It means that, for the first time, perovskite photovoltaics can be genuinely fully roll-to-roll printable (a term often used but, until now, incorrect).
Read the case study on roll-to-roll printed perovskites here.
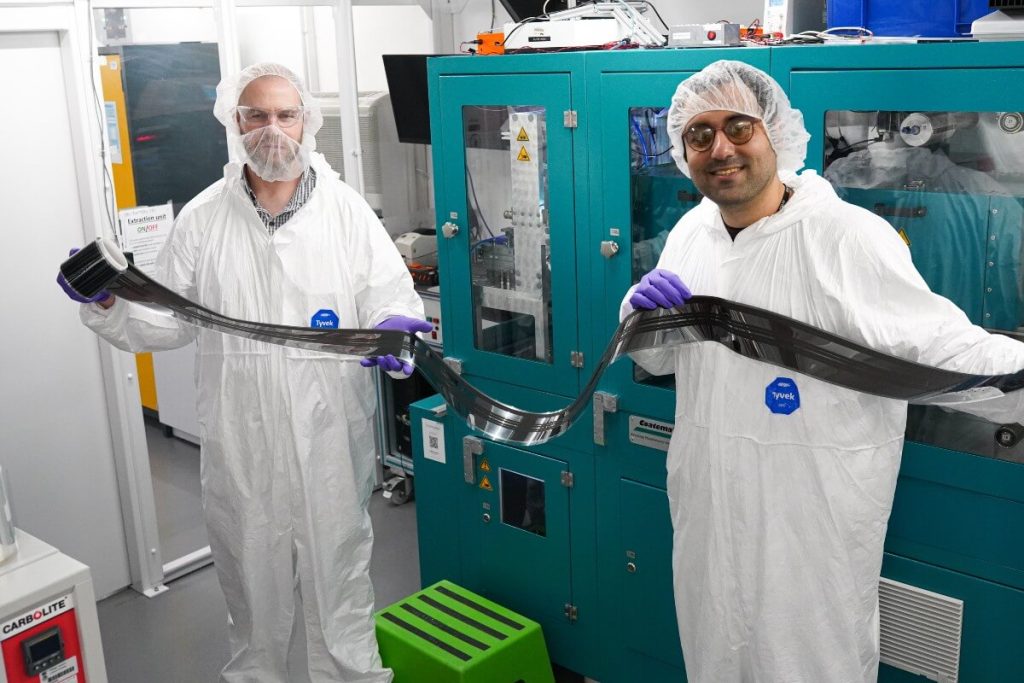
A Safer, Greener Way to Make Solar Cells
Another issue facing printed carbon perovskite photovoltaics is that the solvents used to make them are unsustainable, toxic, or psychoactive.
The SPECIFIC photovoltaics team have introduced a novel, green solvent. This replaces the unsuitable solvents currently used in perovskite solar cells.
Read the case study about safer, greener solar cells here.
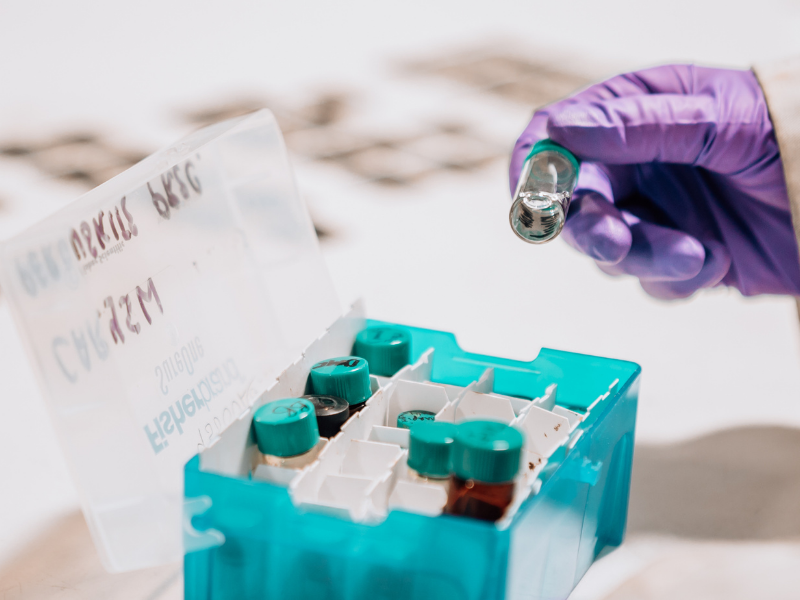
Organic Photovoltaics (OPV) for Indoor Application
Organic solar cells use carbon-based materials and organic electronics – rather than silicon – as a semiconductor to produce electricity from the sun. They are flexible, cheap to produce, and suitable for manufacturing in a printing press, making them competitive with other PV technologies under low light conditions.
At SPECIFIC, we concentrate our research on upscaling, stabilising and using new materials for indoor PV using organic materials. We achieved outstanding indoor performance for OPV solar cells, comparable to the best indoor cells in the market.
Read the case study on organic photovoltaics for indoor application here.
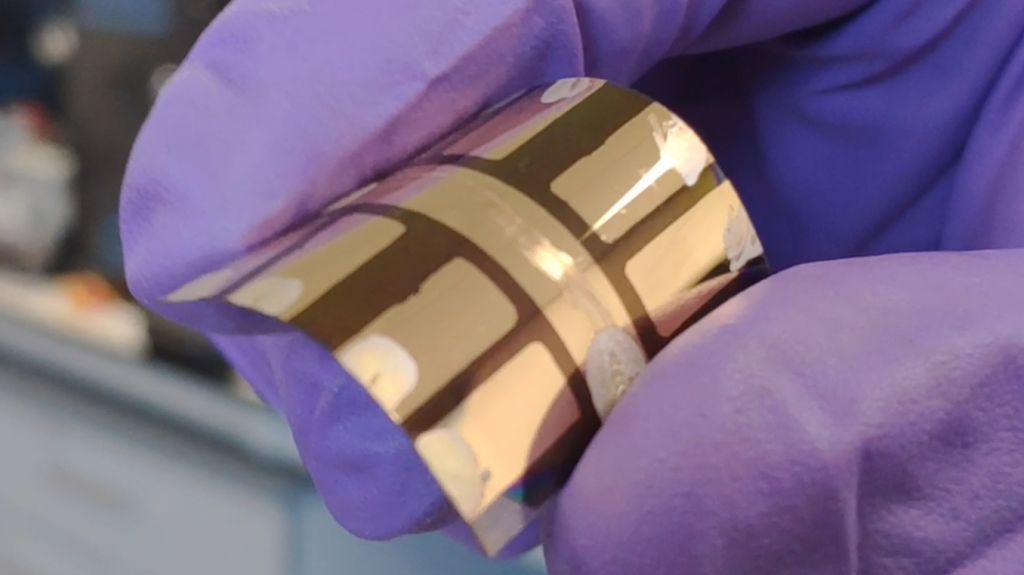
Largest Fully Printed Perovskite Module
Third-generation peroskite solar cells are flexible and lightweight and can be printed onto glass or metal, making them a solution for application in building integrated photovoltaics.
For perovskite solar cells to become commercially viable, they need to be cheap and efficient to manufacture at scale. SPECIFIC’s creation of academia’s largest fully-printed series-connected perovskite module has a 198cm2 active area and over 6.3% efficiency.
Read the case study on our largest fully printed perovskite module here.
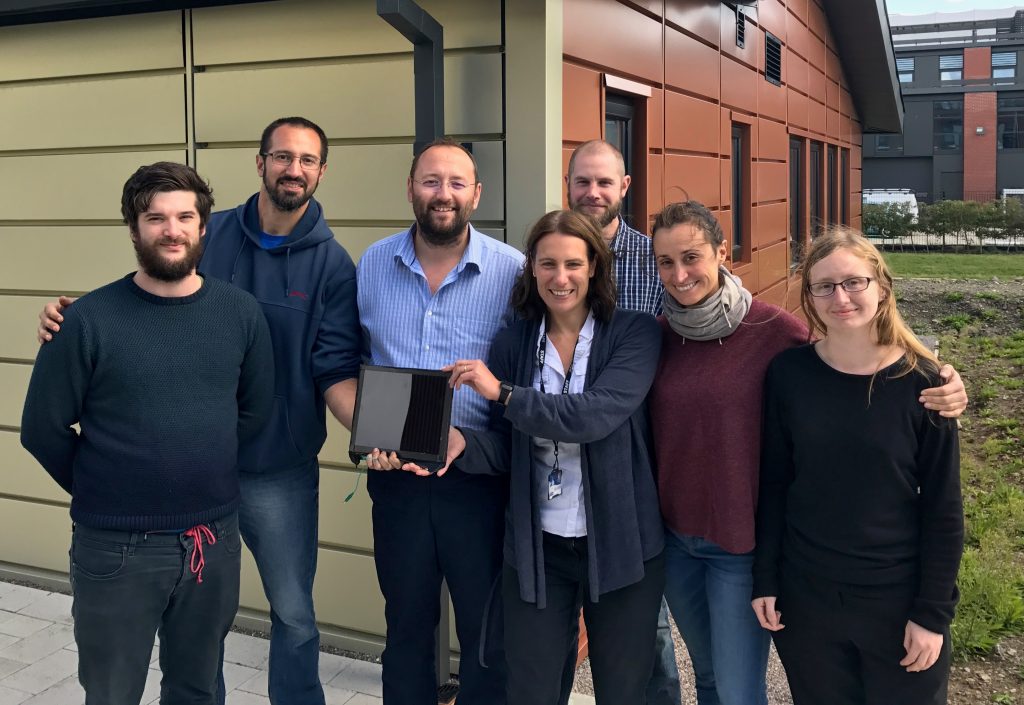
Contacts
- Prof Trystan Watson – Photovoltaics Scale-up and Processing Lead
- Professor Matthew Davies – Applied Photochemistry and the Circular Economy Lead
- Professor Matt Carnie – Photovoltaic Materials, Thermoelectrics and Device Physics Lead
- Dr Wing Chung Tsoi – Organic Photovoltaics and Perovskite Lead
Collaborators: Airbus Endeavr Wales, Armor, Queen Mary University of London, Soochow University, Cinvestav, MIT
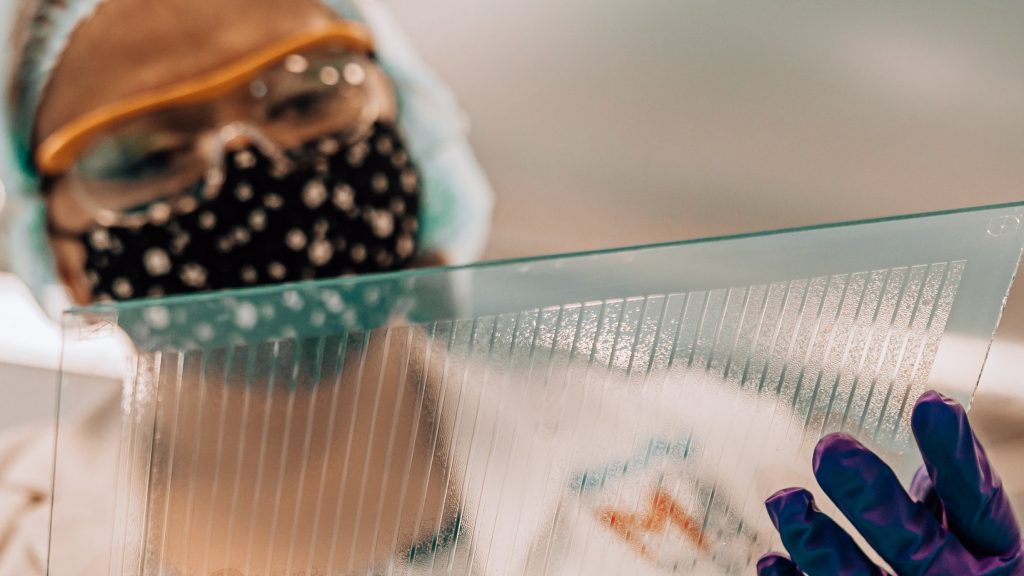
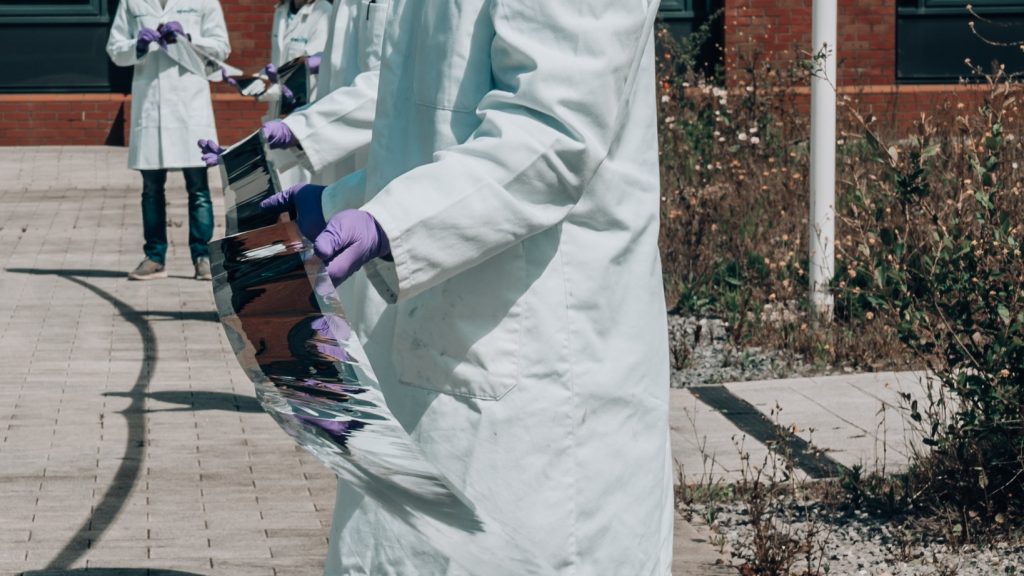